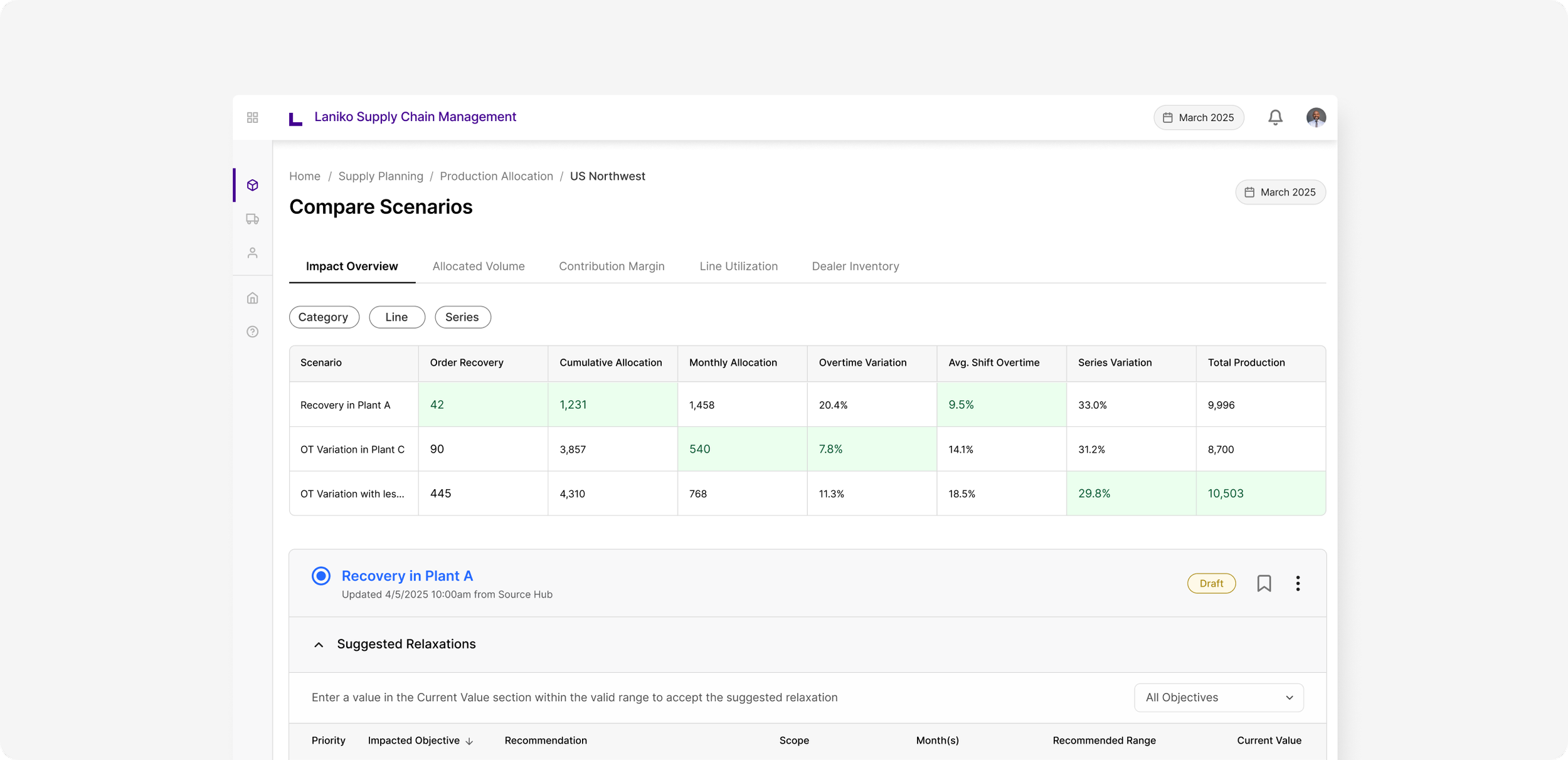
Creating a flexible auto production planning process
Background
A global automaker, Laniko, needed to modernize its auto production planning. The existing process was fragmented across 60+ spreadsheets and 20-year-old systems.
To meet dynamic market demand, we built a Scenario Planning feature as part of a new supply chain suite to enable planners to run what-if simulations, compare outcomes, and make business-backed decisions.
My role
In 16 weeks, I led the product definition, UX/UI design, and backlog creation for Scenario Planning, and collaborated with business leaders, data scientists, and engineers from ideation to launch.
Problem
A journey to unify fragmented planning systems
Lankio, a global auto supplier, was in a company-wide digital supply chain transformation to build long-term resilience and competitiveness in an ever-changing market. At the center of this shift was LPS (Laniko Planning System), a demand-supply planning ecosystem designed to replace decades of legacy systems and manual workflows
The (over)workings of auto production planning
Production planning ran on 75+ spreadsheets, each with its own logic
Planners spent 10+ days a month reconciling data, resolving mismatches, and manually applying 100+ constraints across inventory, capacity, regional rules, and parts
With no shared system or documentation, new hires needed 6+ months to grasp the logic buried in hidden formulas
Solution
From spreadsheets to scenario modeling
The team developed a Scenario Planning module to give planners a way to model production decisions against real-world constraints without starting from scratch or losing control.
Signature Moment 1
Modeling what-ifs from a baseline
Planners started with a baseline plan and could create what-if scenarios by changing key inputs.
The system suggested a recommended range for each input based on real constraints.
As they made changes, planners could instantly see how each scenario affected seven key metrics, such as demand coverage and overtime fluctuation across plants.
Signature Moment 2
Modeling what-ifs from a baseline
With the baseline and what-if scenarios, planners could view how they stack up against historical data and annual production targets.
This comparison view allowed them to assess tradeoffs and spot misalignments without having to chase numbers on spreadsheets, which led to informed planning decisions and confidence to explain those decisions with external teams.
“With business metrics like these, I can have a structured conversation with trainees and incorporate the KPIs into performance reviews… It’s nice to have something other than reviewing spreadsheets.”
— Manager, Production Planning
Signature Moment 3
Keeping planners in control
To build trust and ease the transition from spreadsheets, the MVP kept key parts of the workflow familiar.
Planners could still view and edit individual planning inputs by double-clicking. This interaction gave them direct control and confidence when needed without losing the benefits of automation.
Adoption
Building confidence as an organizational challenge
Planners were deeply skilled but understandably skeptical, and rightfully so. Planners had built their own workarounds over years, and the idea of trusting an automated model felt risky.
A.
For over six months, our team ran every monthly planning cycle in parallel.
We sat with planners one-on-one to walk through their numbers, explain how the model interpreted their constraints, and validate the outcome together.
Ref 4. Production planning parallel run session
B.
This period of handholding helped validate the model, reduce anxiety, and surface gaps in usability. The frequent and consistent interactions with users informed us on design decisions: what needed to stay manual, where visibility was critical, and how to communicate model decisions transparently.
Ref 5. Co-creation and detailed critique sessions with planners and stakeholders
C.
Over time, planners shifted from cautious users to power users and championed the tool across plants and helped drive adoption more broadly.
Ref 6. A planner completed scenario planning and demoed his approach with colleagues
Approach
Designing for trust, clarity, and scale
Design, product, engineering, and data science teams worked on quickly testing, validating, and scaling ideas during planning cycles. Rapid visual iterations, heavy stakeholder involvement and co-creation, and design system scaling played crucial roles in envisioning and creating a new way of working from scratch.
Wireframes as a conversation tool
Wireframes and sketches were a great tool to guide business stakeholders in the future states, as well as the tradeoffs and resources needed to implement their vision. These artifacts were intentionally lightweight to test assumptions and facilitate casual conversations without the feeling of technical commitment.
Design documentation as a product resource
As the project scaled, shifting requirements and cross-functional complexity created gaps. I led an effort to make design documentation the central reference point, which reduced the back-and-forth on minor product decisions during implementation.
Design system built for complexity
I led the expansion of the component library to support increasingly complex workflows and introduced reusable patterns and usage guidelines for faster engineering handoff.
The updated system helped improve velocity and earned praise across Product and Engineering teams.